LATEST Blog
Blog Categories:
All Blog:
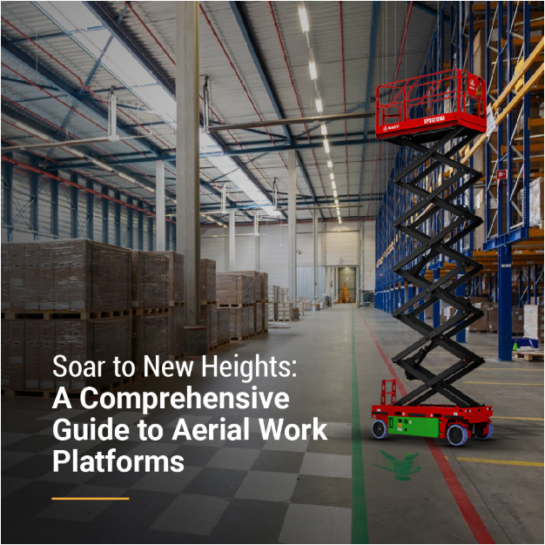
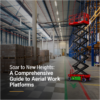
Soar To New Heights: A Comprehensive Guide To Aerial Work Platforms
In the ever-evolving landscape of construction, maintenance, and industrial operations, Aerial Work Platforms (AWPs) play a crucial role in reaching new heights—literally and figuratively. This comprehensive guide delves into the various types of AWPs, their essential safety features, and best practices for maintenance and inspection. Whether you are an industry professional, facility manager, or simply interested in the mechanics of high-access equipment, this guide will provide valuable insights into selecting, operating, and maintaining AWPs to ensure safety, efficiency, and optimal performance. What is an Aerial Work Platform (AWP)? An Aerial Work Platform (AWP) is a mechanical device designed to provide elevated access for personnel and equipment to perform tasks at height. Commonly referred to as aerial lifts, these platforms include various types such as scissor lifts, boom lifts, and personnel lifts. They are equipped with a platform or basket supported by hydraulic, pneumatic, or mechanical systems that allow for vertical and horizontal movement. AWPs are utilized in construction, maintenance, and industrial applications to enhance safety and efficiency when working at elevated positions, adhering to strict safety standards and operational guidelines. Types of Aerial Work Platforms Aerial Work Platforms come in various options, offering easy accessibility for different use cases. Some are optimized for indoor or outdoor use, some for people or equipment, and some for flat or rough surfaces. Here are some of the most common types of Aerial Work Platforms. Scissor Lifts Scissor lifts have a platform that rises vertically using a crisscrossing mechanism of linked, folding supports. They offer stable, high-reaching access for tasks requiring substantial horizontal workspace and are ideal for indoor use or flat surfaces. Boom Lifts Boom lifts feature a platform mounted on an extendable arm or boom, which allows both vertical and horizontal reach. They come in two main types: telescoping (straight) and articulating (knuckle) booms, providing flexibility for accessing hard-to-reach areas. Vertical Mast Lifts These compact lifts have a narrow base and a vertical mast that extends upwards, offering access to high places in tight spaces. They are suitable for indoor applications and are often used for maintenance tasks. Personal Lift Platforms Designed for individual use, these lifts are typically smaller and more portable. They provide access to elevated areas with limited space and are used for tasks like shelving, lighting maintenance, and other small-scale applications. Trailer-Mounted Lifts Also known as tow-behind lifts, these are mounted on a trailer and can be towed…
read more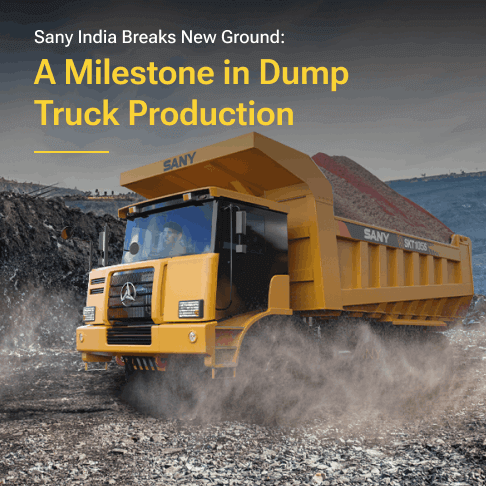
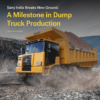
SANY India Breaks New Ground: A Milestone in Dump Truck Production
At SANY India, we’re excited to share a new chapter in our journey—a milestone that reflects our commitment to innovation, quality, and sustainability. With over 1,000 mining dump trucks in our Pune factory, we’re proud to support India’s ‘Make in India’ initiative and drive forward advancements in mining and construction. By setting new standards for durability, fuel efficiency, and operator comfort, we are transforming the mining equipment landscape and contributing to India’s industrial growth. Building India’s Industrial Backbone: SANY’s Journey of Excellence Established in 1989, SANY India has been at the forefront of the global construction and mining equipment industry. Here in India, we’ve built a reputation for delivering top-notch machinery that empowers industries and contributes to the nation’s growth. Our Pune facility is the backbone of this mission, bringing world-class manufacturing and innovation to support India’s rapid industrialisation. A Production Milestone That Speaks Volumes Our recent achievement is truly remarkable. Here’s a closer look at the specifics: Milestone: SANY India’s Pune plant has manufactured over 1,000 mining dump trucks, meeting rising demand in a short span of time. Models Contributing: The milestone includes the production of the SKT90S, SKT105S, and SLT05E models, each designed to meet the needs of India’s mining and construction industries. Timeline: This accomplishment was reached by October, showcasing SANY’s efficient manufacturing capabilities. Production Facility: The Chakan plant in Pune is equipped with advanced machinery and quality control processes. This state-of-the-art facility is instrumental in ensuring every SANY dump truck meets stringent quality standards, aligning with the ‘Make in India’ vision. Driving the Future with Fuel Efficiency and Advanced Engineering SANY India’s mining dump trucks are renowned for technology and innovation. Here’s how each model stands out: Fuel Efficiency: The SKT90S and SKT105S models are designed with fuel efficiency in mind, ensuring lower operational costs even in the harshest conditions. Electric Innovation - SLT05E: The SLT05E model takes efficiency a step further with a regenerative battery that charges itself when descending and consumes minimal energy when ascending. This technology enhances both fuel efficiency and sustainability. Operator Comfort: We understand the importance of comfort for operators working long hours. The trucks feature air-conditioned cabins and ergonomic controls, creating a comfortable and safe workspace. Durability & Continuous Operation: These mining dump trucks are built to work day and night with minimal downtime, ensuring that projects stay on track and productivity remains high. R&D and Quality Standards SANY’s research…
read more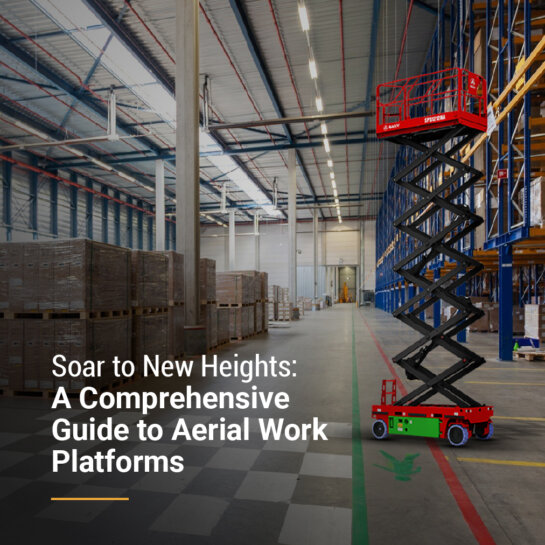
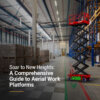
Aerial Work Platforms: Your Essential Selection Checklist
Are you looking for a reliable machine to safely lift workers to perform tasks like repairing overhead electrical wires? For these types of jobs, you require a specialized solution—Aerial Work Platforms. Whether it's for construction, maintenance, or repairs, Aerial Work Platforms (AWPs) are essential tools to ensure safety, increase productivity, and handle tasks at various heights. But with so many options available, how do you know which AWP is the right fit for your project? Let’s dive into this comprehensive guide to help you choose the perfect Aerial Work Platform. What is an Aerial Work Platform? An Aerial Work Platform (AWP) also known as an Elevated Work Platform (EWP) is a mechanical device used to provide temporary access to workers at elevated heights. These platforms are typically equipped with safety features such as guardrails and fall protection systems, allowing workers to safely perform tasks in elevated positions. AWPs are widely used in industries such as construction, maintenance, and warehousing. What are the Major Types of Aerial Work Platforms and Their Applications? When it comes to aerial work platforms, selecting the right one depends on the type of task and the work environment. Below are the major types of aerial lift platforms and their common applications: Telescopic Lifts: Telescopic lifts, also known as straight or stick booms, are perfect for tasks that require extended reach at a fixed height. These are ideal for jobs like tree trimming, construction, and steelwork installations, where a worker needs to access hard-to-reach areas. Boom Lifts: Boom lifts provide more flexibility than telescopic lifts, with extendable arms that can move horizontally and vertically. They are best suited for jobs that require versatile movement, such as electrical maintenance or window cleaning at varying heights and angles. Spider Lifts: Known for their lightweight design and compact structure, spider lifts are perfect for navigating narrow and confined spaces. These lifts are often used in tasks requiring access to difficult areas such as indoor maintenance or confined outdoor spaces. Scissor Lifts: Scissor lifts offer a stable, vertical lifting motion. With a large platform, they are ideal for jobs requiring access to large surface areas at heights, such as painting, roofing, or ceiling installations. Vertical Personnel Lifts: These lifts are lightweight and designed for one person. They are used primarily for indoor jobs like changing light bulbs or performing repairs in warehouses or offices. Articulated Lifts Also known as knuckle booms,…
read more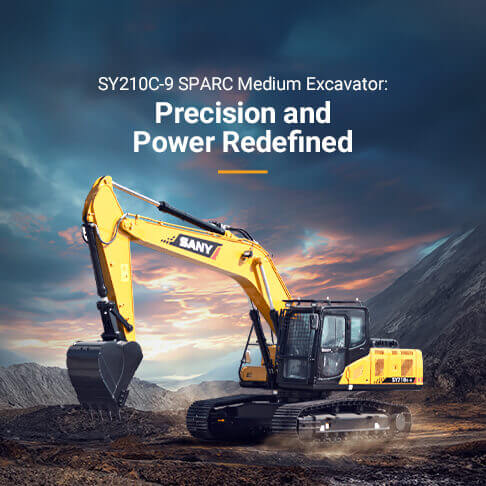
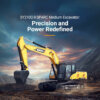
SY210C-9 SPARC Medium Excavator: Precision and Power Redefined
Harness the force of a thunderstorm with the precision of a scalpel—SANY Sparc Medium Excavators deliver raw power that is finely controlled for any challenge. The immense versatility of this machine facilitates its vital role in the construction, mining, and infrastructure sectors. We'll look at SANY’s medium excavator, SY210C-9 SPARC, diving into its unique features that combine advanced technology with robust engineering to ensure it meets the toughest demands. From fuel efficiency and low maintenance costs to intelligent control systems and exceptional durability, let's discover how SANY's medium excavator excels in performance and offers significant cost savings and operational benefits, making it the top choice for professionals in the industry. What are Medium Excavators Used For? Medium excavators are versatile machines that play a critical role in construction, mining, and infrastructure projects. Their mid-sized design lets them handle various tasks that require strength and precision. These machines possess enough power to handle heavy loads, break through tough materials, and perform continuous operations without faltering. Precision is crucial for tasks that require delicate handling, such as trenching near existing structures or grading land with exact specifications. The ability to control such power with finesse ensures that medium excavators can perform a wide range of tasks efficiently. This balance is what sets these medium excavators apart. SY210C-9 SPARC: Robust and Reliable The SY210C-9 SPARC medium excavator, equipped with a Cummins 6BT5.9-C140 engine and weighs 21 tons. It is built for reliability with a strengthened structure and low maintenance cost. This mid-size excavator features DOMCS Intelligent Control and advanced monitoring systems for optimal performance. It ensures exceptional durability through its sturdy undercarriage and robust components, making it well-suited for demanding tasks and challenging environments. This focus on durability is complemented by the machine's design for low maintenance costs, maximizing customer savings through high fuel efficiency and minimal upkeep requirements. The SY210C-9 SPARC leads its class in intelligence and reliability thanks to its advanced monitoring features. Equipped with GPRS monitoring, remote error diagnosis, and smart alerts, which help in providing real-time data and insights. If you are looking for a 20-ton excavator, this might be the perfect choice for you. Fuel Efficiency SANY's medium excavators are equipped with highly efficient engines that significantly reduce fuel consumption, leading to lower operational costs. These engines are designed to optimize power output while minimizing fuel use, ensuring that your projects are both cost-effective and environmentally friendly. This…
read more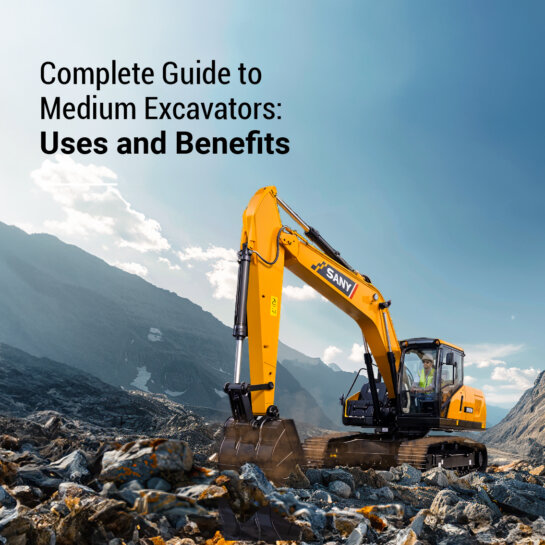
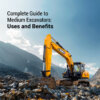
Complete Guide to Medium Excavators: Uses and Benefits
When it comes to tackling the diverse challenges of construction, one piece of equipment stands out for its versatility and power: the medium-sized excavator. Whether you're starting a project, reshaping the land, or lifting heavy materials, medium excavators are the backbone of construction. In this blog, we will discuss the mid-size excavator's types and sizes, applications and benefits. Apart from this, you will get tips for selecting the right mid-size excavator for your business. Mid-size Excavators Mid-size excavators, often referred to as medium excavators are typically crawler excavators with weights ranging between 15 to 34 tons. These excavators are versatile machines that balance the power of larger excavators with the maneuverability of smaller ones. Mid-size excavators provide an ideal balance of power and maneuverability, making them versatile tools for a wide range of tasks such as digging, trenching, and demolition. Their compact size allows them to operate effectively in confined spaces, while still delivering the strength required for demanding jobs. Additionally, they are cost-effective, with lower fuel consumption and maintenance needs, and are easier to transport compared to larger machines. With advanced cab features and the ability to use various attachments, mid-size excavators enhance productivity and adaptability, making them a valuable asset for diverse construction, landscaping, and utility projects. Where Do We Use Mid-size Excavators? Mid-size excavators are a popular choice in many industries due to their versatility, power, and ability to operate in both large and confined spaces. Here are some tasks for which the mid-size excavator is the ideal option: Construction Sites: Mid-size excavators are widely used in general construction projects. Their size allows them to perform tasks such as digging foundations, trenching, and grading with efficiency. Landscaping: They are also popular in landscaping projects where they are used for tasks like moving soil, creating ponds, or removing trees and large stumps. Road Construction: In road construction, mid-size excavators are used for digging trenches for utilities, removing pavement, or grading road surfaces. Utility Work: These machines are ideal for utility installation projects, such as laying pipes or cables, because they offer enough power to dig deep trenches while remaining compact enough to operate in tighter spaces. Demolition: Mid-size excavators are often employed in demolition projects where they can tear down small to medium-sized structures, break up concrete, and remove debris. Mining and Quarrying: In smaller mining and quarrying operations, mid-size excavators are used for tasks such as digging…
read more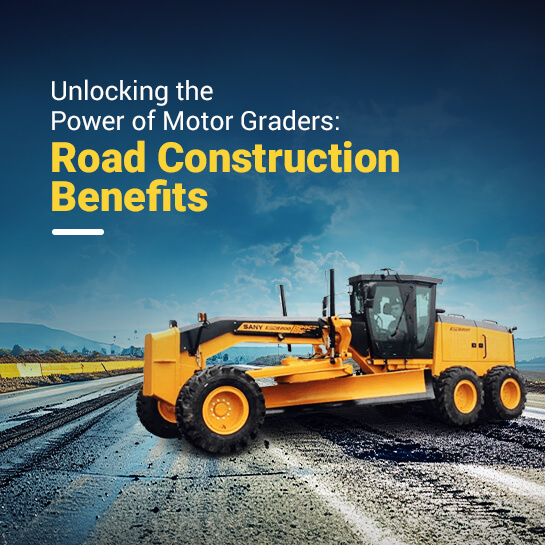
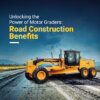
Unlocking the Power of Motor Graders: Road Construction Benefits
In the world of road construction, the motor grader stands out as a key player, an indispensable tool that ensures the smoothness, precision, and durability of our roadways. Whether you're a seasoned contractor or a newcomer to the construction industry, understanding the importance and capabilities of motor graders is crucial. This blog will delve into the essential features of motor grader machines, their role in road construction projects, and the numerous benefits they offer, from precision grading to enhanced efficiency. What is a Motor Grader? It is a heavy construction machine equipped with a long blade used to create a flat surface during the grading process. Motor grader equipment is typically utilized in the construction and maintenance of roads, offering the precision needed to achieve a smooth and even surface, which is vital for road quality and longevity. Essential Features of Motor Grader Equipment Motor graders are designed with several features that make them indispensable in road construction: Precision Grading: The primary function of a motor grader machine is to create a level surface. The blade of a motor grader can be adjusted to various angles, pitches, and heights, allowing operators to grade with exceptional accuracy. This precision is essential for laying a stable foundation for roads, ensuring that the surface is even and properly contoured to support subsequent layers of asphalt or concrete. Durability: Motor grader equipment is built to withstand the rigors of tough construction environments. With robust engines and high-quality materials, these machines are designed for long-term use. Their durability not only reduces the frequency of maintenance but also ensures consistent performance across multiple projects. Versatility: Motor graders are incredibly versatile. They can be used for a variety of tasks beyond road construction, such as leveling soil, and spreading materials. This versatility makes them a valuable investment for construction companies, as they can be used year-round for different applications. Advanced Technology: Modern motor grader machines come equipped with advanced technology, such as GPS and laser systems, which further enhance their precision and efficiency. These technologies allow operators to execute complex grading tasks with ease, reducing the likelihood of errors and the need for rework. Benefits of Using Motor Graders in Road Construction The benefits of using motor graders in road construction projects are manifold. Here’s how these machines contribute to the success of such projects: Enhanced Efficiency: Motor graders streamline the grading process, making it faster and…
read more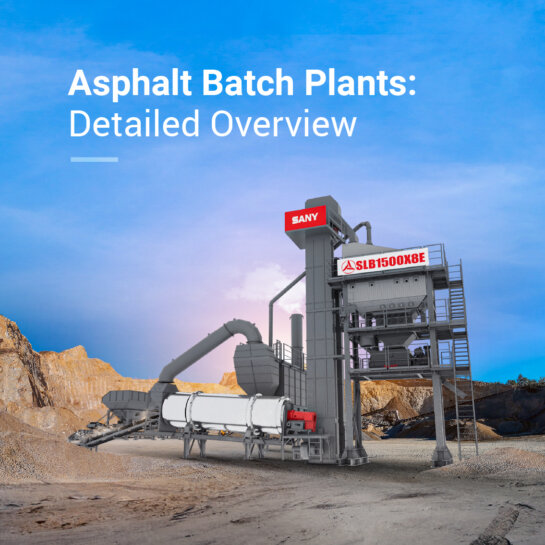
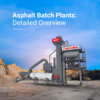
A Complete Guide to Understanding Asphalt Batch Plants
Understanding the asphalt batch plant ensures the production of high-quality asphalt, which is essential for creating durable and long-lasting roads. Not only that, it also enhances efficiency by optimizing the use of materials for road construction. This knowledge is key to maintaining strict quality control, reducing the risk of defects, and assuring the asphalt meets specific project requirements. In this blog, we will explore asphalt batch plants, their working principles, and their essential role in successful construction projects, contributing to improved roads and infrastructure. What is an Asphalt Batch Plant? An asphalt batch plant is a facility that produces hot mix asphalt in batches rather than in a continuous process. These plants are highly flexible and capable of producing different types of asphalt mixtures, such as hot mix asphalt (HMA), warm mix asphalt (WMA), and cold mix asphalt (CMA). The versatility and precision in the mixing process make asphalt batch plants ideal for various road construction projects, ranging from small repairs to large highway developments. Key components of Asphalt Batch Plant Here are the various key components of the Asphalt Batch Plant: Cold Feeder Bins: These bins store different sizes of aggregates and feed them into the system in controlled amounts. They ensure a steady and precise supply of raw materials to the drying drum. Conveyor: A conveyor belt transports the cold aggregates from the feeder bins to the dryer drum. It facilitates continuous movement and consistent feed of aggregates into the system. Drying Drum: The drying drum heats the aggregates to remove moisture and achieve the desired temperature. It is equipped with a powerful burner to ensure efficient heating. Elevator: This component lifts the heated aggregates from the drying drum to the vibrating screen. It ensures the smooth transfer of materials for further processing. Vibrating Screen: The vibrating screen separates the hot mix into various compartments based on size. It ensures precise classification of aggregates before mixing. Hot Bins: Hot bins temporarily store the heated and classified aggregates before they are weighed. They ensure the availability of the right amount of materials for mixing. Weighing Systems: These systems measure precise amounts of filler, aggregate, and bitumen. They are crucial for maintaining the correct proportions in the asphalt mix. Pugmill Mixing Unit: The pugmill mixing unit thoroughly mixes the weighed ingredients to create the hot mix asphalt. It ensures a homogeneous and high-quality mix. Dust Collection System: This system collects…
read more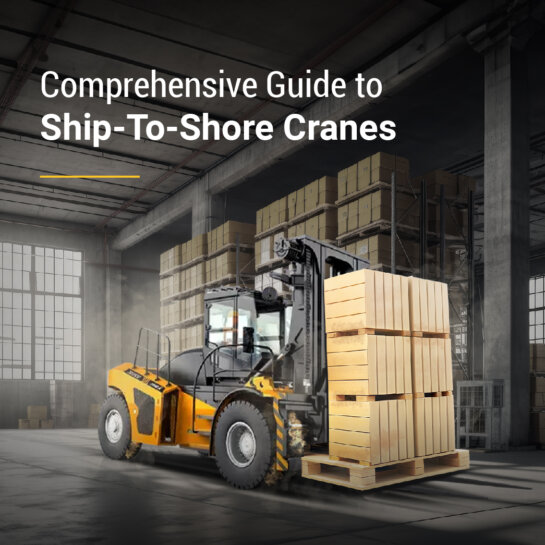
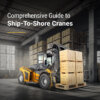
Comprehensive Guide to Ship-To-Shore Cranes
Ship-to-shore cranes are pivotal in modern port and terminal operations, playing a crucial role in the efficient handling of cargo between ships and the dock. These massive structures are designed specifically to load and unload container ships, making them an essential component in the global logistics chain. Their primary function is to transfer containers from vessels to the shore and vice versa, ensuring a seamless flow of goods. Understanding the intricacies of ship-to-shore cranes is vital for professionals in the maritime and logistics industries, as their importance extends beyond mere cargo handling to significantly impact the speed, safety, and efficiency of port operations. By the end of this guide, you will have a thorough understanding of ship-to-shore cranes, enabling you to appreciate their critical role in maritime operations and make informed decisions in your professional endeavours. Types of Ship-To-Shore Cranes Rubber-Tyred Gantry (RTG) Cranes Rubber-Tyred Gantry (RTG) cranes are highly versatile cranes mounted on rubber tyres, allowing them to move freely within a port or terminal. They are commonly used for stacking and moving containers in container yards. Their mobility makes them ideal for operations that require flexibility and adaptability in container handling. Rail-Mounted Gantry (RMG) Cranes Rail-Mounted Gantry (RMG) cranes operate on fixed rails, providing stability and efficiency in container handling operations. They are typically used in larger ports and terminals with high throughput requirements. RMG cranes are ideal for repetitive and high-volume container stacking and retrieval tasks. Fixed and Mobile Cranes Fixed cranes are stationary and mounted in a fixed position, typically used for specific tasks such as loading and unloading ships. Mobile cranes, on the other hand, can be moved and repositioned as needed, providing flexibility for various operations within the port. Ship to Shore Crane Specifications Structure and Design: The structure and design of ship-to-shore cranes are critical to their functionality and efficiency. The main structural elements include the boom, which extends over the ship to reach the containers, and the girder, which supports the boom. The legs or columns provide stability, while the trolley runs along the boom to transport containers between the ship and the shore. These cranes are typically constructed from high-strength steel to ensure durability and withstand the heavy loads they are required to handle. The materials used must resist corrosion, given the harsh maritime environment, and maintain structural integrity under constant use. Operating Mechanisms: The operating mechanisms of a ship-to-shore crane…
read more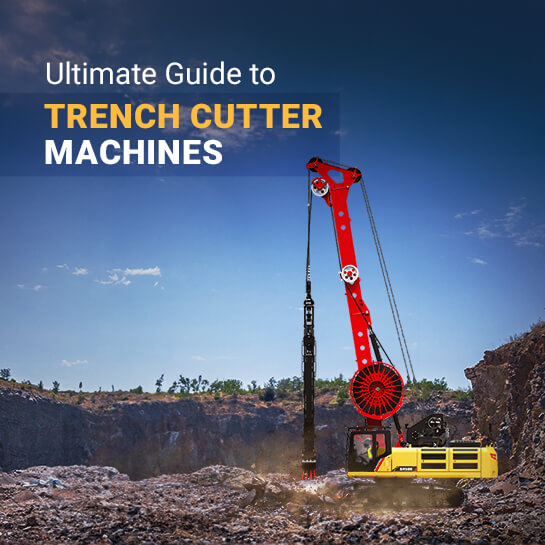
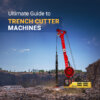
The Complete Guide to Trench Cutter Machines
When a construction site requires the excavation of deep trenches, such as those reaching depths of 120 meters with precision, traditional excavators are not sufficient. For these demanding tasks, you need a dedicated trench cutter machine designed specifically to dig deep trenches with accuracy and efficiency. Whether it's constructing diaphragm walls or laying foundations in challenging ground conditions, trench cutters offer unparalleled precision and effectiveness. In this guide, we will discuss trench cutters, their major applications, and the benefits that make them indispensable in today's construction industry. What are Trench Cutter Machines? Trench cutter machines are specialized pieces of equipment used in civil engineering and construction for creating deep, narrow trenches in various types of ground conditions. These machines are equipped with powerful cutting wheels or chains that can excavate hard soil, rock, and other dense materials with precision, making them essential for constructing deep foundations, slurry walls, and other subterranean structures. Major Applications of Trench Cutter Here are some major applications of trench cutters on the job site: Diaphragm Walls Trench cutter machines are extensively used in constructing diaphragm walls, which are essential for deep foundations in large buildings and infrastructure projects. Slurry Walls for Environmental Containment Trench cutters play a vital role in creating slurry walls, which are used to contain contaminants and control groundwater flow in environmental engineering projects. Foundations for Dams and Hydraulic Structures In the construction of dams and hydraulic structures, trench cutters are employed to create deep, narrow trenches that serve as foundations. Retaining Walls and Cut-off Walls Trench cutter machines are used to build retaining walls and cut-off walls, which are necessary for stabilizing slopes and preventing landslides. Underground Facilities and Tunnels For underground facilities and tunnel construction, trench cutters are utilized to create precise, deep trenches needed for the foundations and structural supports. Key Benefits of Using a Trench Cutter on the Job Site Here are some of the key benefits of utilizing trench cutter machines for construction project: Precision and Accuracy Trench cutter machines provide exceptional precision and accuracy in creating deep, narrow trenches. This ensures that construction projects adhere to exact specifications, reducing the risk of structural issues and costly rework. Efficiency and Speed The powerful cutting mechanisms of trench cutters enable rapid excavation of hard soil, rock, and other materials. This significantly speeds up the construction process, allowing projects to stay on schedule and reduce labor costs. Versatility in…
read more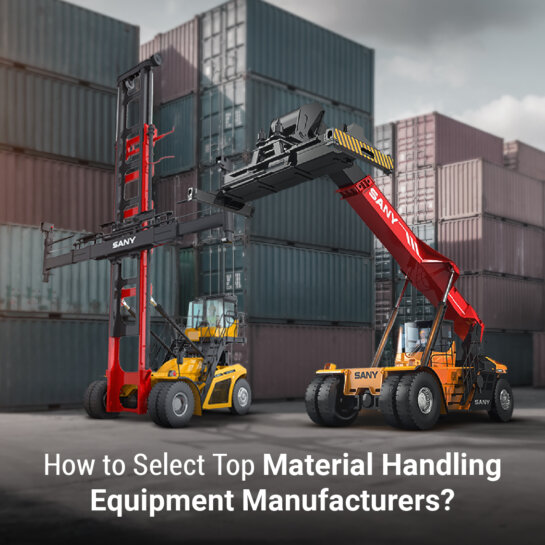
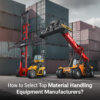
How to Select the Best Material Handling Equipment Manufacturer?
When it comes to material handling equipment, choosing the right manufacturer can make all the difference. High-quality equipment can streamline your operations, improve efficiency, and reduce costs. However, with so many manufacturers out there, how do you determine which one is the best for your needs? This guide will provide you with essential criteria to consider when selecting top material handling equipment manufacturers, including insights into Sany's product offerings, specifications, and details. Criteria for Choosing the Best Material Handling Equipment Manufacturers 1. Innovation and Technology Innovation is a key factor in determining the quality of material-handling equipment. Manufacturers that prioritise research and development (R&D) tend to offer more advanced, efficient, and durable products. Look for manufacturers that integrate the latest technology in their equipment, such as automation, IoT (Internet of Things), and AI (Artificial Intelligence). 2. Product Quality and Durability The quality and durability of the equipment are paramount. You need equipment that can withstand harsh working conditions and deliver consistent performance over time. Evaluate the materials used, the manufacturing process, and the overall build quality of the equipment. 3. Range of Products A diverse product range indicates a manufacturer's capability to meet various material handling needs. Check if the manufacturer offers a wide selection of equipment types, such as forklifts, cranes, conveyors, and excavators, to cater to different industries and applications. 4. Customer Service and Support Excellent customer service and support are critical when selecting a manufacturer. This includes pre-sale consultation, after-sale service, maintenance, and parts availability. A responsive and supportive customer service team can significantly enhance your equipment's lifecycle and operational efficiency. 5. Reputation and Reliability A manufacturer's reputation in the market is a strong indicator of its reliability. Research customer reviews, testimonials, and case studies to gauge the experiences of other users. Additionally, check for industry awards and recognitions that highlight the manufacturer's credibility. 6. Cost-effectiveness While the initial cost of material handling equipment is important, it’s crucial to consider the total cost of ownership. This includes maintenance costs, energy efficiency, and the potential for downtime. Opting for slightly more expensive equipment that offers better performance and lower operational costs can be more economical in the long run. 7. Customisation Options Different operations have unique requirements, and the ability to customise equipment to fit specific needs can be a significant advantage. Check if the manufacturer offers customisation options, such as different attachments, sizes, and capabilities. 8. Environmental…
read more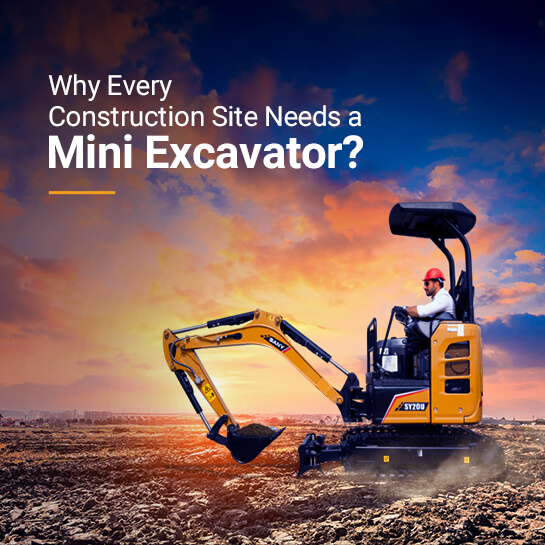
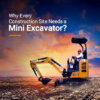
The Advantages of Mini Excavators in Construction Operations
In the dynamic world of construction, mini excavators emerge as the unsung heroes, bringing a host of advantages to the table over their larger counterparts. Just as a knife excels in precision tasks that a sword would find difficult to handle, these small excavators are perfect for navigating tight spaces, making them indispensable for urban construction projects. These underdogs of the construction world pack a powerful punch despite their small size. Keep reading to discover how mini excavators are making a big impact on construction projects of all sizes. What are the Different Varieties of Mini Excavators? Here are the different varieties of mini excavators based on their size ranges: Small Mini Excavators: Comprising the majority of available models, small mini excavators typically offer dig depths ranging from 5 to 10 feet and dump heights between 6 to 11 feet. With horsepower ranging from 10 to 40 hp, these agile machines, weighing approximately 900 to 4,500 kg, excel in tight spaces and delicate foundation work. Medium Mini Excavators: Medium compact excavators display impressive dig depths up to 15 feet, dump heights reaching 21 feet, and engine power up to 74 hp. Weighing between 4,500 to 9,000 kg, these machines offer versatility across various construction projects, often matching or exceeding larger classes in performance. Large Mini Excavators: Though fewer in number, large mini excavators achieve dig depths exceeding 17 feet and maximum dump heights of 20 feet, with horsepower ranging from 69 to 75 hp. Weighing over 9,000 kg, these powerful machines are ideal for projects requiring substantial force, ensuring efficiency in demanding construction tasks. What is a mini excavator used for? Mini excavators are versatile machines used for various construction, landscaping, and utility tasks. Some common mini excavator uses include: Digging: Mini excavators excel at digging tasks, including excavating foundations, trenches for utility lines, or holes for landscaping features like ponds or trees. Demolition: With the right attachments, mini excavators can be used for selective demolition tasks, such as breaking up concrete, removing small structures, or clearing debris. Landscaping: Mini excavators are invaluable for landscaping projects, such as grading terrain, shaping slopes, installing retaining walls, or creating garden beds. Utility Work: They are often employed for installing underground utilities like water pipes, sewer lines, electrical conduits, and drainage systems. Material Handling: Mini excavators equipped with grapples or buckets can efficiently handle materials like gravel, soil, sand, and debris, making them…
read more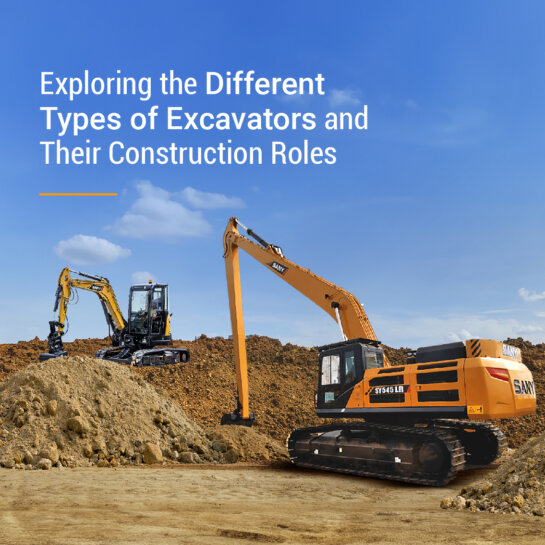
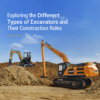
Discovering the Various Types of Excavators and Their Contributions to Construction
Starting a construction project without an excavator is like setting sail without a compass – it's possible, but certainly not recommended. These powerful machines excel in tasks ranging from digging foundations and trenches to loading and lifting heavy materials. However, their effectiveness is not one-size-fits-all, leading to the necessity of different types of excavators tailored to specific jobs and environments. From compact mini excavators ideal for confined spaces to massive hydraulic excavators suited for large-scale projects, each excavator type offers unique capabilities crucial for diverse construction needs. Furthermore, the wide range of excavator attachments further enhances their adaptability, enabling them to undertake numerous tasks with precision and speed. In this blog, we will explore various types of excavators and the different attachments used for excavator application. Types of Excavator Machines Here are various types of excavators used in construction sites: Wheeled Excavators Wheel excavators are distinguished by their wheeled mobility, offering exceptional speed and maneuverability, particularly suited for road construction and urban development projects. Equipped with rotating platforms, arms, and buckets, they efficiently dig, lift, and move materials across varied terrain. Their ability to navigate paved surfaces and uneven ground makes them versatile for a range of construction projects. Application: Ideal for road construction, urban development, and applications requiring quick mobility. Long-Reach Excavators Long-reach excavators, featuring extended arms and booms, are specialized machines designed for deep digging, dredging, and demolition tasks. Their extended reach capabilities enable access to difficult areas such as deep trenches and tall structures, maintaining stability and control while operating at extended distances. They are valuable assets in projects involving waterway maintenance, bridge construction, and selective demolition. Application: Useful in tasks requiring deep excavation, dredging, or demolition work. Mini Excavators Mini excavators are smaller and lighter versions of standard excavators, designed to minimize ground damage and navigate crowded, narrow sites with ease. They often feature reduced tail-swing or zero tail-swing configurations, allowing them to maneuver tight turns and avoid obstacles effectively. Application: Frequently used in parking lots, indoor spaces, and other cramped sites where standard excavators may not fit. Small Excavators Small excavators are compact yet powerful machines designed for small to medium-sized projects. They offer excellent versatility and efficiency, making them suitable for a wide range of tasks in confined spaces. Application: Ideal for utility work, residential projects, and landscaping tasks. Medium Excavators Medium excavators strike a balance between size and power, providing robust performance for…
read more