A Complete Guide to Understanding Asphalt Batch Plants
Category: Uncategorized | 26 July 2024
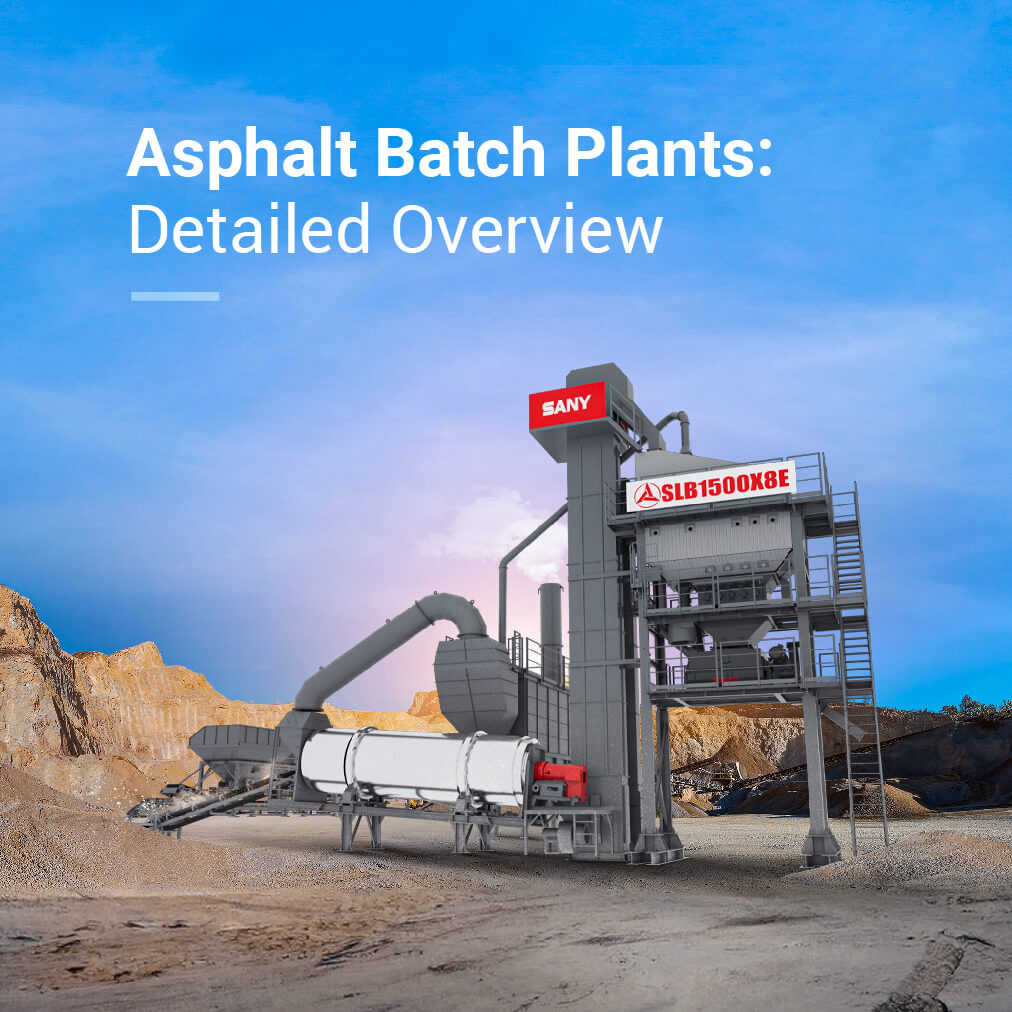
Understanding the asphalt batch plant ensures the production of high-quality asphalt, which is essential for creating durable and long-lasting roads. Not only that, it also enhances efficiency by optimizing the use of materials for road construction.
This knowledge is key to maintaining strict quality control, reducing the risk of defects, and assuring the asphalt meets specific project requirements. In this blog, we will explore asphalt batch plants, their working principles, and their essential role in successful construction projects, contributing to improved roads and infrastructure.
What is an Asphalt Batch Plant?
An asphalt batch plant is a facility that produces hot mix asphalt in batches rather than in a continuous process. These plants are highly flexible and capable of producing different types of asphalt mixtures, such as hot mix asphalt (HMA), warm mix asphalt (WMA), and cold mix asphalt (CMA). The versatility and precision in the mixing process make asphalt batch plants ideal for various road construction projects, ranging from small repairs to large highway developments.
Key components of Asphalt Batch Plant
Here are the various key components of the Asphalt Batch Plant:
Cold Feeder Bins: These bins store different sizes of aggregates and feed them into the system in controlled amounts. They ensure a steady and precise supply of raw materials to the drying drum.
Conveyor: A conveyor belt transports the cold aggregates from the feeder bins to the dryer drum. It facilitates continuous movement and consistent feed of aggregates into the system.
Drying Drum: The drying drum heats the aggregates to remove moisture and achieve the desired temperature. It is equipped with a powerful burner to ensure efficient heating.
Elevator: This component lifts the heated aggregates from the drying drum to the vibrating screen. It ensures the smooth transfer of materials for further processing.
Vibrating Screen: The vibrating screen separates the hot mix into various compartments based on size. It ensures precise classification of aggregates before mixing.
Hot Bins: Hot bins temporarily store the heated and classified aggregates before they are weighed. They ensure the availability of the right amount of materials for mixing.
Weighing Systems: These systems measure precise amounts of filler, aggregate, and bitumen. They are crucial for maintaining the correct proportions in the asphalt mix.
Pugmill Mixing Unit: The pugmill mixing unit thoroughly mixes the weighed ingredients to create the hot mix asphalt. It ensures a homogeneous and high-quality mix.
Dust Collection System: This system collects and removes dust from the mix, ensuring environmental compliance and reducing pollution. It typically includes dry dust collectors.
Control System: An advanced control system provides both manual and automated control over various parts of the plant. It allows operators to monitor and adjust operations for optimal performance.
Working Principle of Asphalt Batch Plant
An asphalt batch plant operates by producing hot mix asphalt in batches, ensuring precise control over the mix composition. The process begins with aggregates stored in cold feeder bins, where they are measured and transferred to the drying drum via a conveyor. In the drying drum, aggregates are heated to remove moisture using a powerful burner. The heated aggregates are then lifted by an elevator to the vibrating screen, which separates them into various sizes for storage in hot bins.
Next, specific proportions of aggregates, bitumen, and filler materials are weighed and fed into the pugmill mixing unit. The pug mill thoroughly mixes these ingredients to create a homogenous hot mix asphalt. This mix is stored in a heated storage silo until it is ready to be loaded into trucks for transportation to the construction site. This batching process allows for precise adjustments and high-quality control, ensuring the production of asphalt that meets specific project requirements.
Why Asphalt Batch Plants are Essential for Construction Projects
Here are the key reasons why these plants are crucial for road construction projects:
Quality Control
Asphalt batch plants offer precise control over the composition and quality of the asphalt mix. This ensures the production of durable and high-performance asphalt, which is crucial for various road construction projects that need to withstand heavy traffic and harsh weather conditions.
Versatility
These plants can produce different types of asphalt mixtures, such as hot mix asphalt (HMA), warm mix asphalt (WMA), and cold mix asphalt (CMA). This flexibility makes them suitable for a wide range of applications, from small patching jobs to large highway projects.
Cost-Effectiveness
Asphalt batch plants are cost-effective in the long run due to efficient resource utilization, including aggregates, bitumen, and energy. Producing asphalt on-site reduces transportation costs and improves profitability for road construction projects.
Environmental Benefits
Modern asphalt batch plants incorporate technologies like baghouse filters to minimize emissions of dust, smoke, and odors. Additionally, using warm mix asphalt technology reduces greenhouse gas emissions and energy consumption, contributing to environmental sustainability.
Use of Recycled Materials
These plants can incorporate a high percentage of reclaimed asphalt pavement (RAP), allowing old roads to be recycled into new ones. This not only reduces production costs but also conserves natural resources by reusing existing materials.
Customization
Asphalt batch plants allow for easy adjustments and customizations based on project requirements. This means that specific mix designs can be achieved efficiently, ensuring that the asphalt produced meets the exact needs of each construction project.
To Conclude
Asphalt batch plants are essential for construction projects due to their ability to produce high-quality asphalt mixtures with precision ensuring the durability and productivity in road construction projects.
Sany India is renowned as one of the leading asphalt mixing plant manufacturers in India. Our asphalt batch plant SLB1500X8E is designed to deliver superior performance with a capacity of 120T/h at 3% moisture content. With a maximum total power of 275 kW, this plant is engineered for efficiency and productivity. Our advanced design reduces preparation time by 15% and increases fuel efficiency by 10%, ensuring cost-effective and environmentally friendly operations.
Choose Sany India's Asphalt Batch Plant for unparalleled reliability and efficiency in your road construction projects.
