Tips to Get the Most Out of Your Excavator Rock Breaker
Category: Excavators | 08 June 2023
The construction equipment industry in India is poised for good times ahead after surviving the present pandemic situation. In fact, as per the TechSci Research report i.e., India Construction Equipment Market by segment, product type, region, competition, forecast & opportunities, 2025, “Construction equipment industry in India is projected to cross $ 4.7 billion by 2025 on account of anticipated growth in the construction industry, increasing foreign investments and rising number of smart city projects in the country. Further, government initiatives focused on infrastructure development is also expected to boost the demand for various types of construction machines in India and same holds true for excavators.
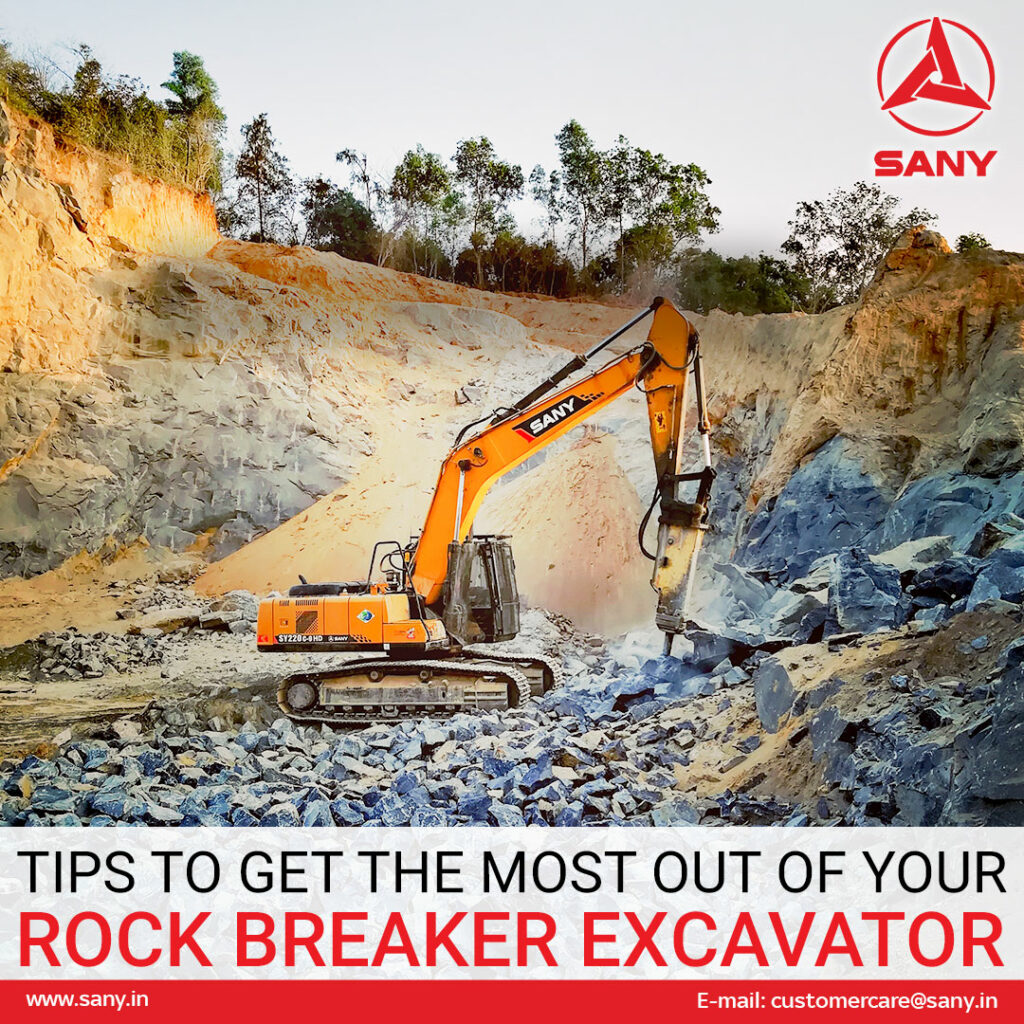
Best used for digging and moving large objects among various other tasks that they perform, excavators are widely used in Quarry, Urban construction, Infrastructure, house building, road construction, landscape engineering, mining and so on. They offer excellent performance and versatility at the jobsite due to the various attachments. In fact, it is these various useful excavator attachments that make them reliable enough to handle various tasks in different working environments. Also, these attachments add to the overall productivity of the excavators. Amongst the various attachments, excavator-mounted hydraulic rock breakers deserve a special mention.
Also called as hydraulic hammers, rock breakers are best for breaking hard objects like rock, concrete, asphalt and other construction and aggregate materials. Rock breakers are powered by the hydraulic energy. A hydraulic hammer to break rocks and a robust housing bracket are two major components of the rock breakers.
Getting the best out of your excavator rock breaker
Excavator-mounted rock breakers are designed in such a way that they can withstand toughest operating conditions, However, their excessive usage can result in wear and tear. So, in order to achieve the most from the excavator-mounted rock breakers, their maintenance is very important as without that there might be project delays, wastage of time and money and the lifespan of the attachment may also reduce. So, here are some top tips through which you can get the optimal performance, increase the life of your excavator rock breaker and get the most out of it...
- Visual inspection is necessary: In order to check the rock breaker for any wear and tear, visual inspection after every use is a must. However, this step is often overlooked but this should not happen as thorough visual inspection, you can easily identify any worn or damaged components on time and prevent unexpected downtime. Hydraulic hoses, the breaker Housing, attachment pins, Chisel pins and locks and the tool point for any cracks or gouges should be considered in the visual inspection checklist.
- Hydraulic hoses should be examined carefully: You need to check that the hydraulic hoses from the excavators are of correct length and always routed properly. This is because hoses that are short in length restrict attachment extension and hoses longer in length can become disengaged on rebar and other debris.
- The importance of greasing the excavator-mounted rock breaker: Greasing at regular intervals assumes lot of importance because it helps in lubricating and clearing the tool bushing area of debris. For greasing, the manufacturer’s recommendations must be followed. This is because if the grease is added before properly positioning the breaker, it could lead to seal damage or even a catastrophic failure and too little grease could cause the bushings to overheat, seize and damage tools. So, in the best case scenario, greasing should be done every one to two hours to reduce build-up, tool wear and bushing wear.
- Checking the nitrogen pressure: It is important to maintain proper nitrogen pressure in rock breaker Head cap and accumulator, and this depends on the application and outside working temperature. As a matter of fact, the nitrogen level required for breaking rocks is different from what is required for breaking concrete in a parking lot. Here, the attachment’s operation and maintenance manual can come to help as it will have the details about the nitrogen pressure setting for your application and working temperature.
- Regular checks are also needed: The hydraulic breaker is percussion equipment, the bolts and nuts can easily become loosened, which is the cause of severe damage to several component parts. Thus, check torque of nuts, bolts periodically, as per the guidelines shared by manufactures. Regular checking of the wear status of the chisel, bushes and chisel pin is very important as excessive wear of bushes and chisel can cause chisel head and piston damage.
- Regular servicing is the key: If the rock breaker is serviced regularly, its durability can increase considerably. However, if there are issues, rock breakers can be repaired or rebuild to give the best results.
Apart from the above, the other few things that should be kept in mind to get the best out of your excavator-mounted rock breaker include the following tips:
- Insufficient Thrust: To break effectively, a proper thrust force has to be applied to the breaker.
- Excessive Thrust: If the breaker chisel down thrust force is excessive, If hammering is performed under such a condition, vibrations may also be transmitted to the tracks, therefore, hammering in such a manner should be avoided
- The direction of Thrust: Apply thrust in a straight line with the tool. Place the tool on a rock with the hammering side as vertically as possible.
- Stop the operation as soon as the rock breaker hoses vibrate excessively
- Do not move/leverage rocks with a rock breaker chisel.
- Operate the breaker at a proper engine speed recommended by OEM
- Do not operate the breaker in water and mud.
- Changes in Hydraulic service Intervals: To Achieve the best working efficiency and life of hydraulic excavator and breaker, follow the hydraulic service intervals changes recommended by the OEM for the equipments working with rock breaker.
- You need to always read the rock breaker specifications written in the owner’s manuals, catalogues, and brochures and follow the instructions.
- Operator training is a must. Operators should be trained to properly position the rock breaker to optimize productivity and minimize stress on the attachment and excavator.
- You should never use the rock breaker in a ‘lever’ motion or drop it on an object that is to be broken as it can damage the excavator as well as its rock breaker attachment.
- You should never operate the excavator-mounted rock breaker at one spot for long as it can increase the hydraulic temperature.
- In order to achieve the best working efficiency, you should move the impact point from the edge to the centre.
- Knowing that hydraulic breaker attachments are not universal in size, you need to ensure that rock breaker for the excavator is properly sized for it so as to increase excavator’s performance for breaking material. If the breaker is too large for the excavator, the energy can be displaced and this can diminish the breaker’s impact on the material if the breaker is too small, it can put excessive pressure on the working steel and other mounting components, potentially causing damage.In order to achieve the best working efficiency, you should move the impact point from the edge to the centre.
Thus, by following the above-mentioned tips, you can ensure that your excavator-mounted rock breaker gives maximum result at the jobsite and its life is extended considerably. While there are many companies that offer excavator-mounted rock breakers, Sany India deserves a special mention here as definitely Sany India’s excavator-mounted rock breakers can be your best bet for applications such as rock cutting, road cutting and demolitions. Versatile with attachments like rock breakers, the range of excavators i.e., mini, small, medium, and large as well as wheeled excavators manufactured by Sany are highly stable, fuel-efficient, reliable, and durable, require minimum maintenance and have a long shelf life and give excellent results in terms of performance and unmatched productivity.
To sum up...
In the future, the major drivers for construction machines in India including excavator rock breaker would be the growing road, construction, and infrastructure industry and the positive outlook of the mining industry. So, it is best to add the excavator-mounted rock breaker to your fleet now to keep up with the growing demand of the future.
